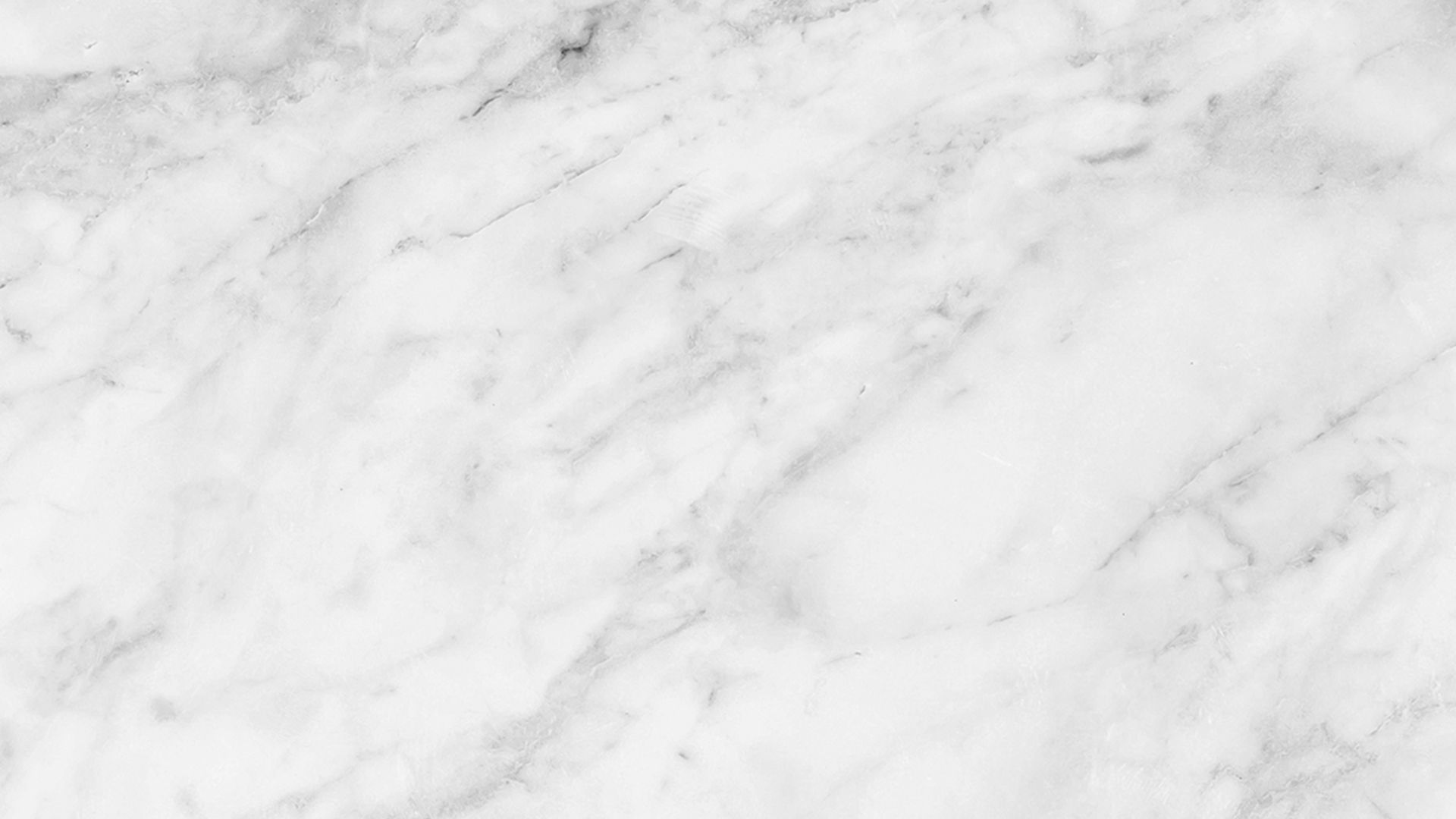
Our Technology
3D MultiMat™ Printer
B.M.P.D
Bound Materials Paste Deposition
Bound Metal Paste Deposition or BMPD is our primary proprietary feedstock and is loaded in our 950ml container/extruder assembly. This feedstock is extremely easy to load and totally safe in any office or workshop environment.
The unique technology of the 3D MultiMat™ BMPD primary feedstock is due to the use of a solvent based binder, most of the binder evaporates quickly during the printing and at rest time after the printing. No necessity for a first stage debinding. Any residual binder is removed during its time in the sintering furnace.
This makes our 3D MultiMat™ printer the fastest - by skipping a long step in the process of going from initial design to fully finished part.
​
The advantages
​
The Metallic 3D print system eliminates the expensive lasers, poorly packed, dusting powder beds, poor strength of parts, no need for a debinding wash or necessity of Hot Isostatic Pressing (HIP), large footprints, daunting cost of operation and maintenance. This affordable, tough printer can be used to manufacture complex parts with geometries that traditional manufacturing methods are unable to produce or the part is too costly to produce. We have a material range that includes difficult to process materials so you can manufacture overall better parts of metal or many other materials, such as superalloys or technical ceramics for your business or clients.
​
​
Our desktop printer is up to 10x less expensive than alternative metal additive manufacturing technologies and up to 100x less traditional fabrication technologies like machining or casting. This gives the owner of a Metallic 3D printer a higher ROI, less time making parts and less worries over quality. All you need is power and an internet connection to get started in Additive Manufacturing metal printing.
​
​
​
​
​
Parts printed with the conventional three-stage process need to be debound from the polymerbinder. This step can take up to 50 hours, and may require processing the part in a toxic chemical solvent, a messy and dangerous process in any office environment. Our BMPD method is the safest and most environmentally friendly method of handling the materials for 3D metal printing. No fumes or odors are created in the printer during the print process. Our Metallic 3D printer includes our proprietary software with a perpetual license and free updates as needed.
​
​
​
The 3D MultiMat™ printing process can be used to manufacture complex, bespoke parts with geometries that traditional manufacturing methods are unable to produce today. The 3D printed parts can be topologically optimized to maximize their performance while minimizing their weight and the total number of components in an assembly, reducing cost. 3D MultiMat™ printed parts have excellent physical properties and the available material range includes difficult to process otherwise materials, from superalloys to advanced technical ceramics which can offer a wide range of properties, depending on the industrial functionality task involved.